This section provides the description of some distributed parameter control problems. These examples can be also viewed through DPS Examples block.
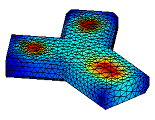
Control of the temperature field in the volume of complex shape metal body
Complex shape metal body is being heated through contact heating elements on subdomains Ω1 – Ω4. Distributed transient characteristics (transient responses) are numerically calculated in COMSOL software. The dynamics of control inputs comprises of actuating member transfer functions SA(s), input generator transfer functions SG(s) and shaping units T. The control task is to bring the temperature field to a new steady state by means of PID control synthesis.
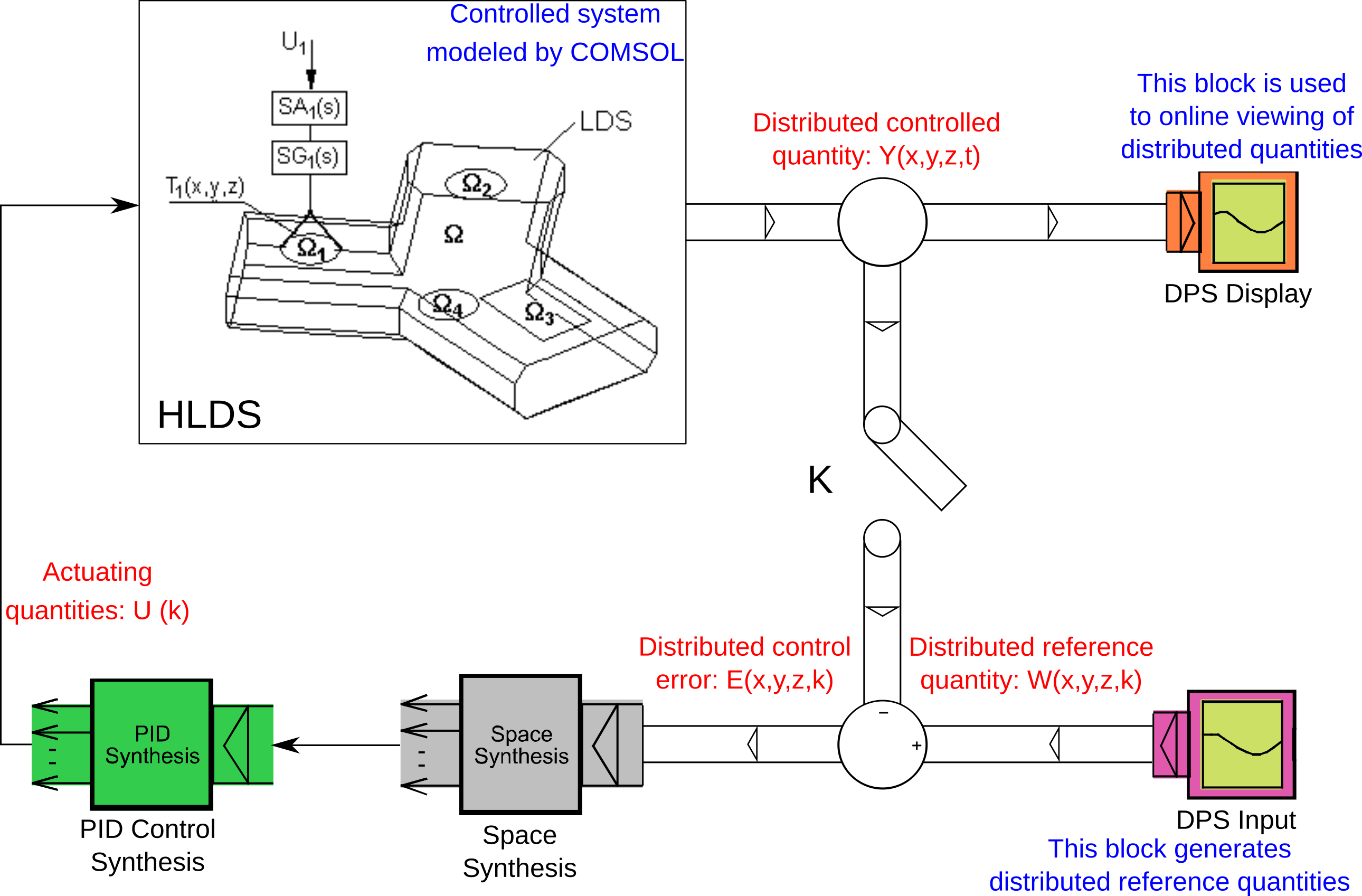
Legend
Ω – definition domain of the heated body
Ωi – i-th subdomain of the heating element (i-th boundary condition region)
SAi – i-th transfer function of the actuating member (voltage source time-dynamics)
SGi – i-th transfer function of the distributed input generator (heating element time-dynamics)
Ui – i-th lumped input quantity (i-th control input, voltage)
Ti – i-th shaping unit (heat flux distribution over subdomain region)
HLDS – lumped input / distributed output system (voltage / temperature field)
K – sampling (Simulink inherited)
Model data
Material – steel (98.5 Fe, 1.3C, 0.1Si, 0.1Mn)
Number of lumped inputs – 4, individually controlled
Ti (x, y, z), i = 1,2 and 4 – conical shape
Ti (x, y, z), i = 3 – pyramidal shape
SAi , i = 1,2,3 and 4 – const = 1 (neglected time-dynamics, immediate reactions)
SGi , i = 1,2,3 and 4 – const = 1 (neglected time-dynamics, immediate reactions)
Distributed transient characteristics (system dynamics identification)
U1 – control voltage step change / temperature field transient response
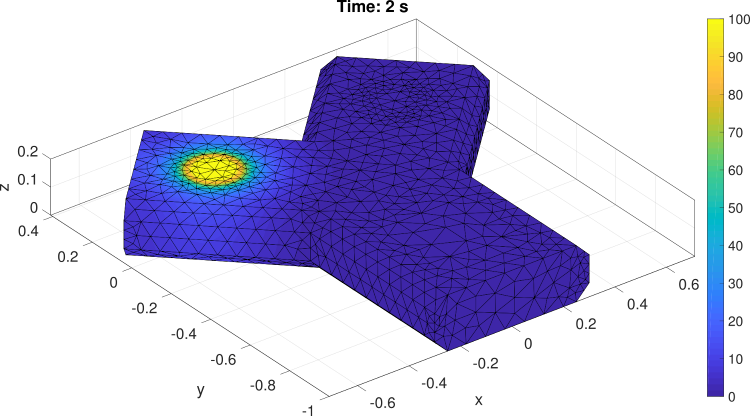
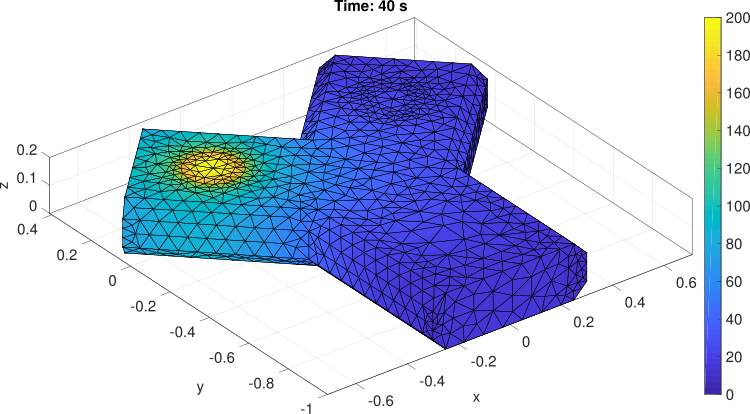
U2 – control voltage step change / temperature field transient response
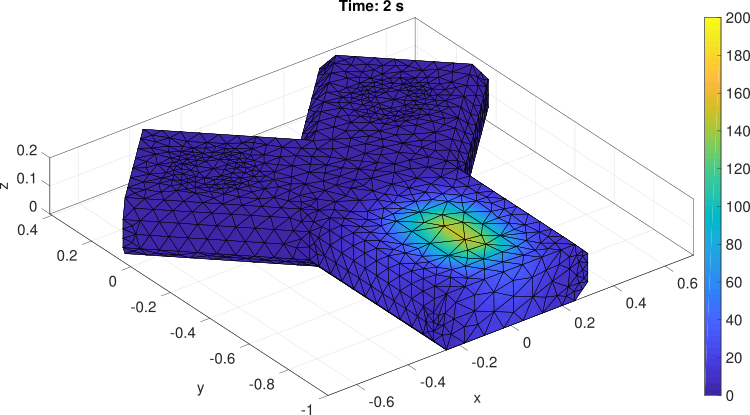
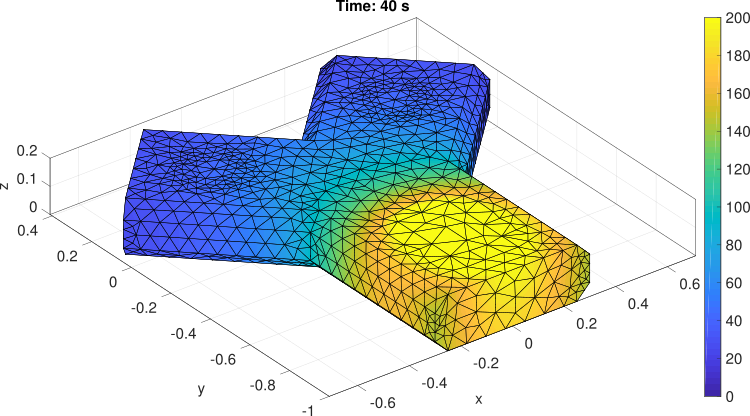
U3 – control voltage step change / temperature field transient response
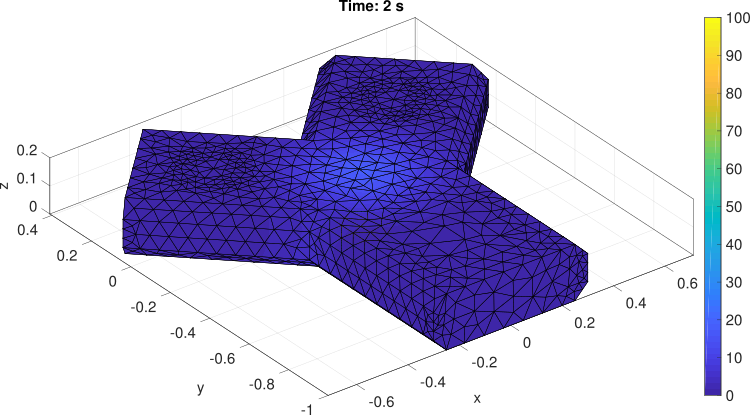
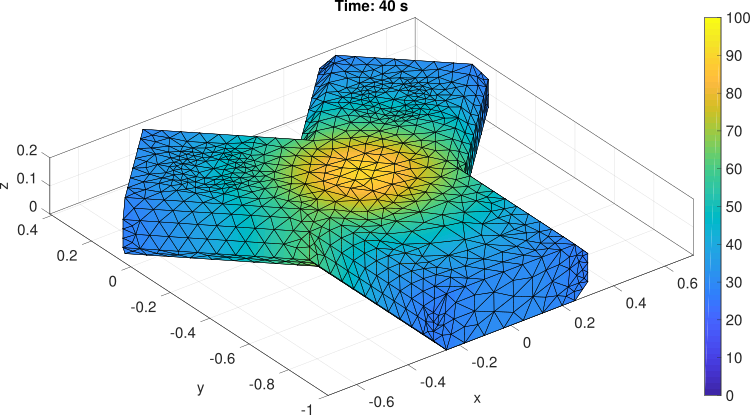
U4 – control voltage step change / temperature field transient response
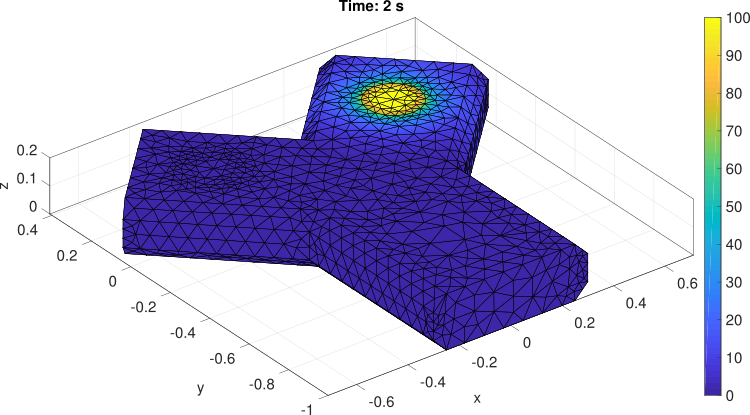
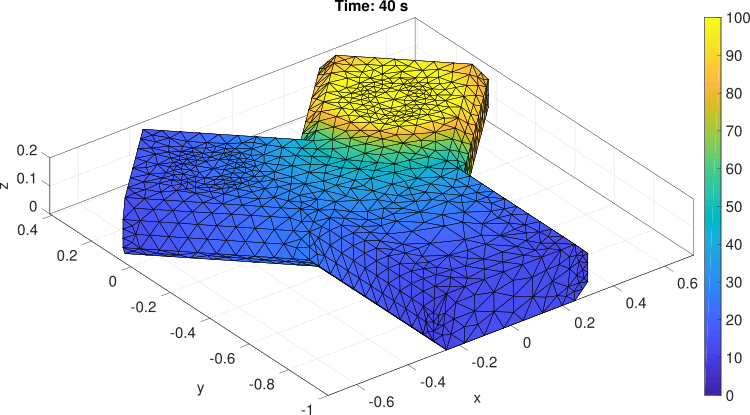
Control process (reaching a new steady-state temperature field)
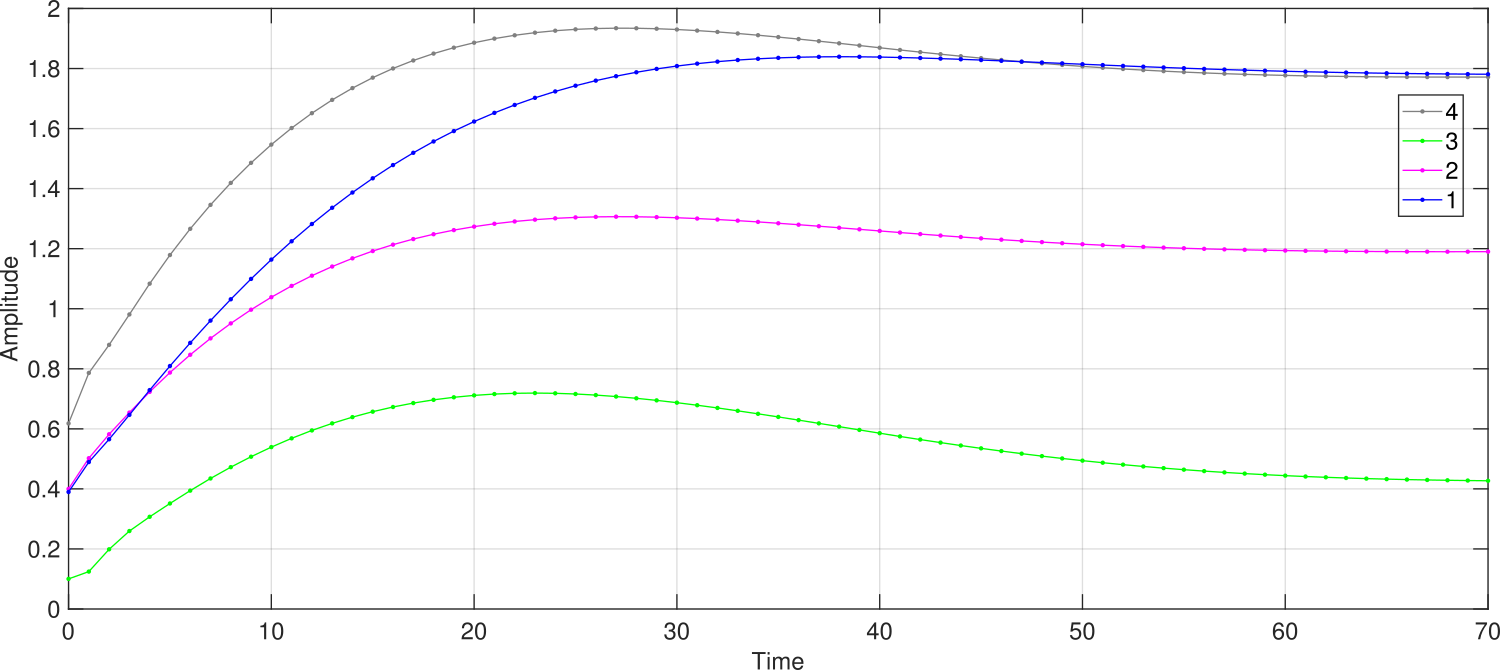
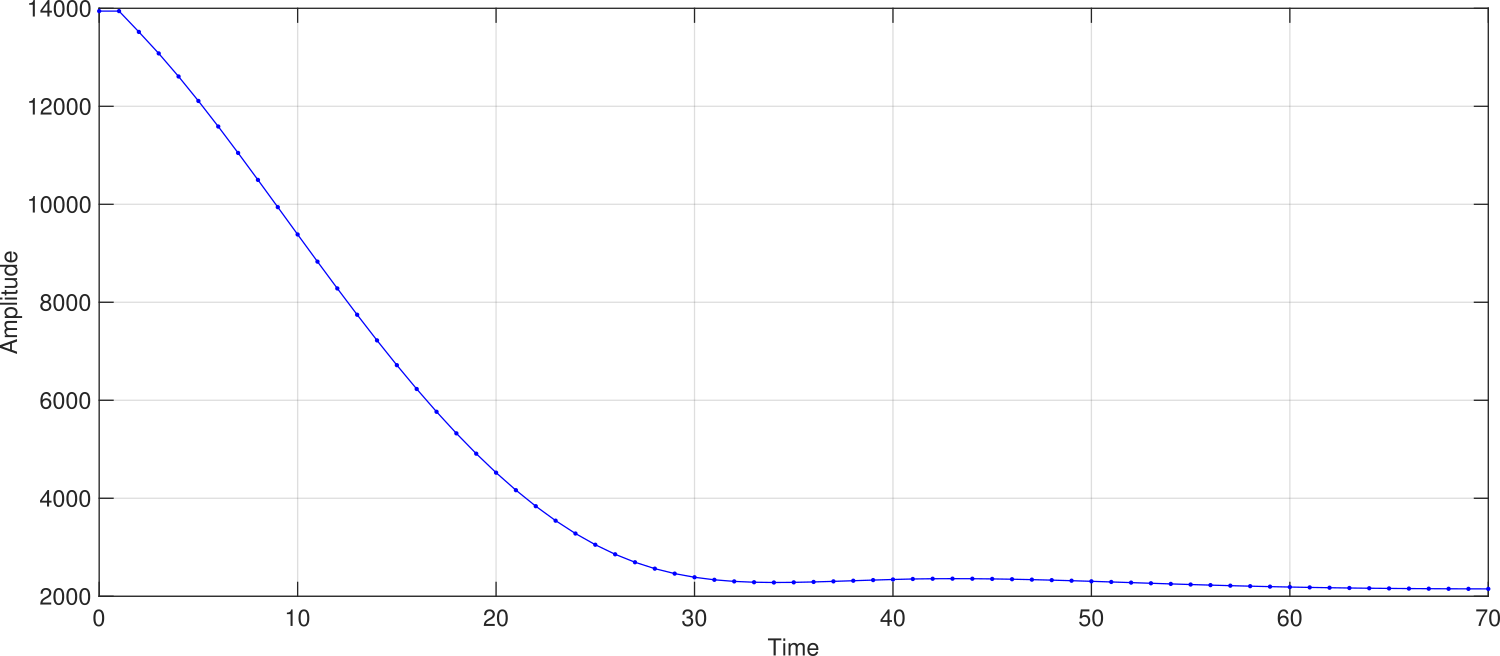
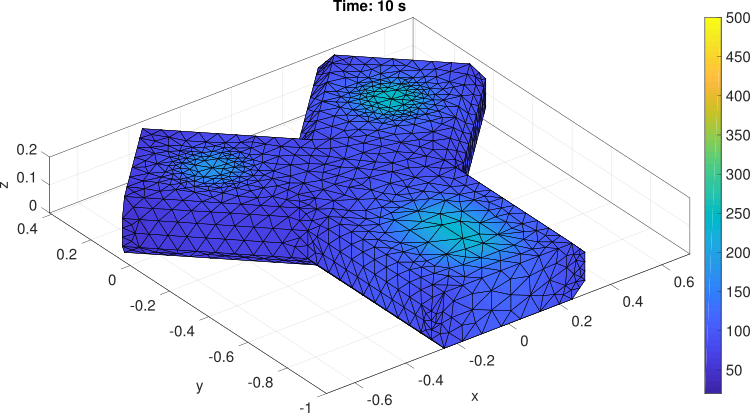
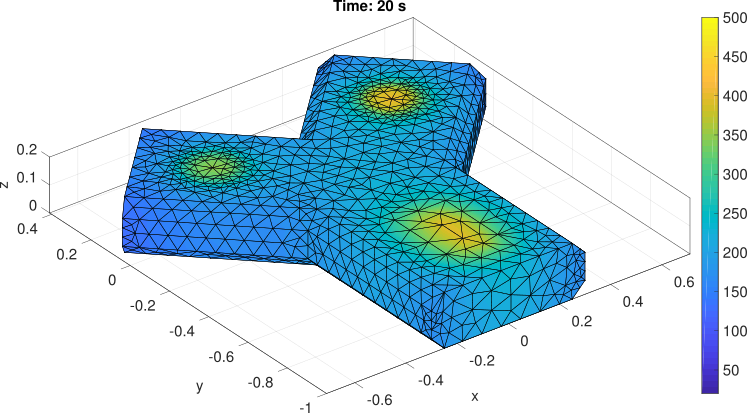
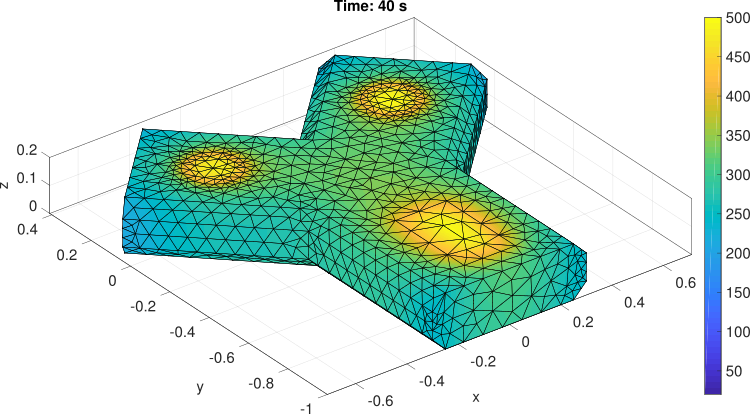
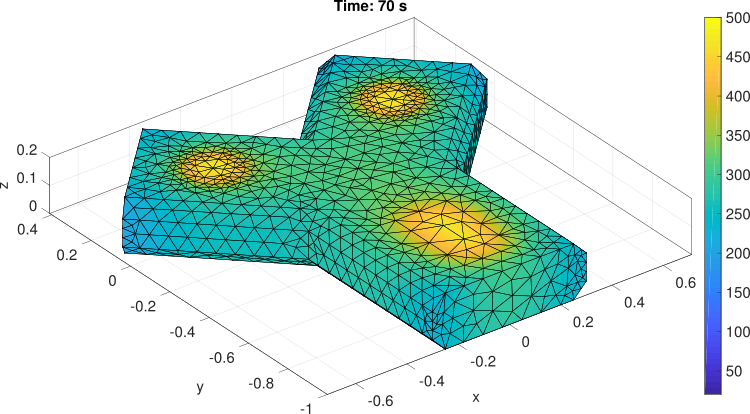

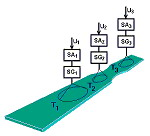
Oscillation control of the „smart“ structure beam
Complex shape metal beam is being deflected using piezoceramic actuators attached to subdomains Ω1 – Ω3. Distributed transient characteristics (transient responses) are numerically calculated in ANSYS software. The dynamics of control inputs comprises of actuating member transfer functions SA(s), input generator transfer functions SG(s) and shaping units T. The control task is to bring the beam into a new steady state shape by means of PID control synthesis.
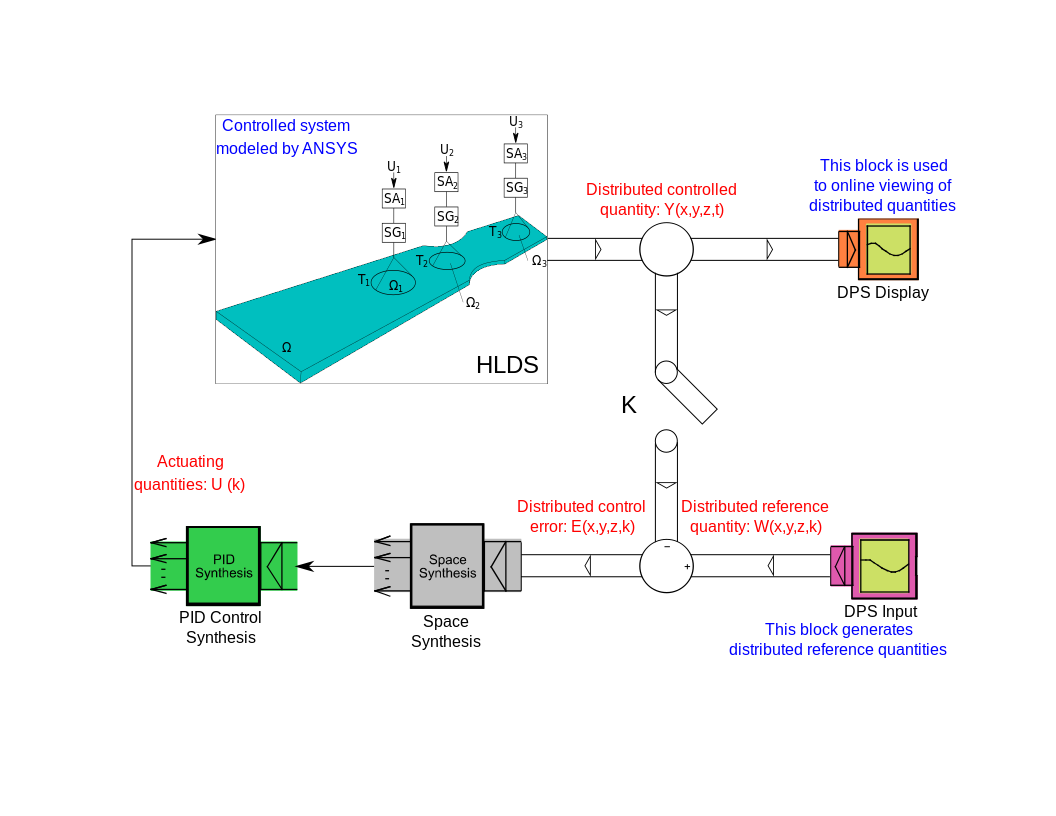
Legend
Ω – definition domain of the metal beam
Ωi – i-th subdomain of the piezo element (i-th boundary condition region)
SAi – i-th transfer function of the actuating member (voltage source time-dynamics)
SGi – i-th transfer function of the distributed input generator (piezo element time-dynamics)
Ui – i-th lumped input quantity (i-th control input, voltage)
Ti – i-th shaping unit (load distribution over subdomain region)
HLDS – lumped input / distributed output system (voltage / displacement)
K – sampling (Simulink inherited)
Model data
Material – aluminium alloy
Number of lumped inputs – 3, individually controlled
Ti (x, y, z), i = 1,2 and 3 – conical shape
SAi , i = 1,2,3 – const = 1 (neglected time-dynamics, immediate reactions)
SGi , i = 1,2,3 – const = 1 (neglected time-dynamics, immediate reactions)
Distributed transient characteristics (system dynamics identification)
U1 – control voltage step change / displacement transient response
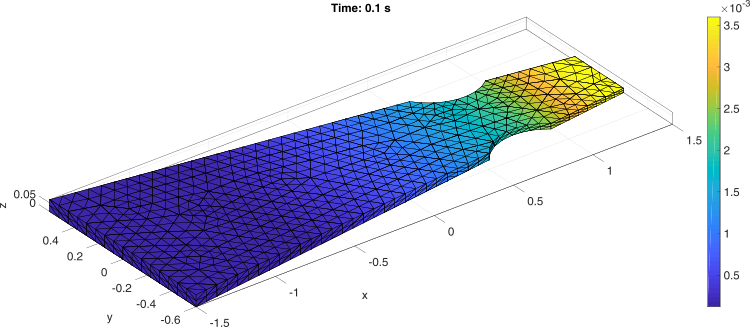
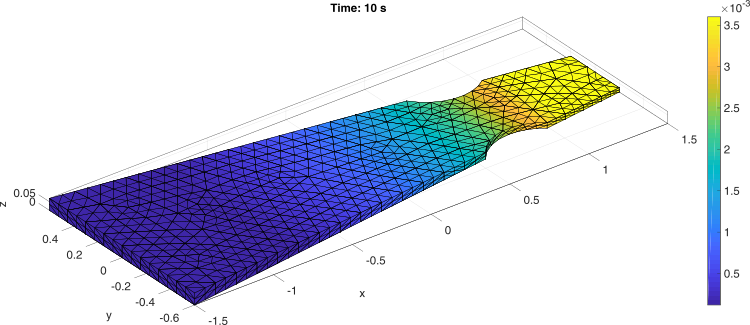
U2 – control voltage step change / displacement transient response

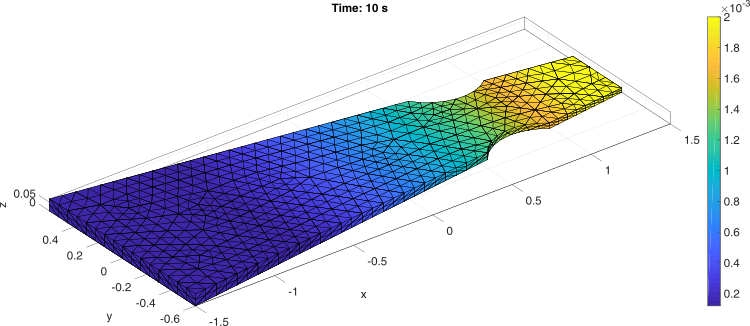
U3 – control voltage step change / displacement transient response
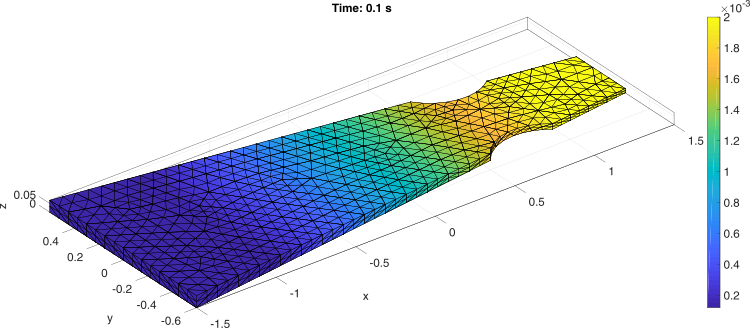
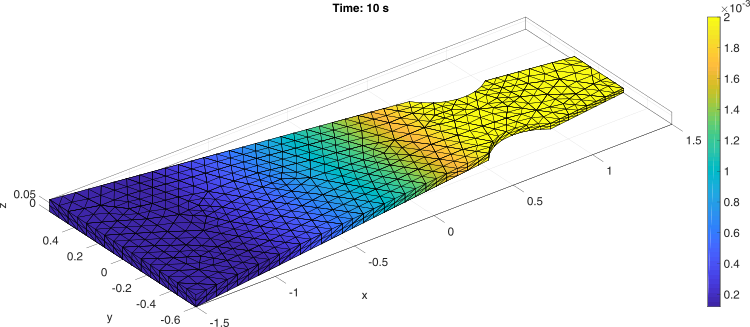
Control process (reaching a new steady-state displacement field)
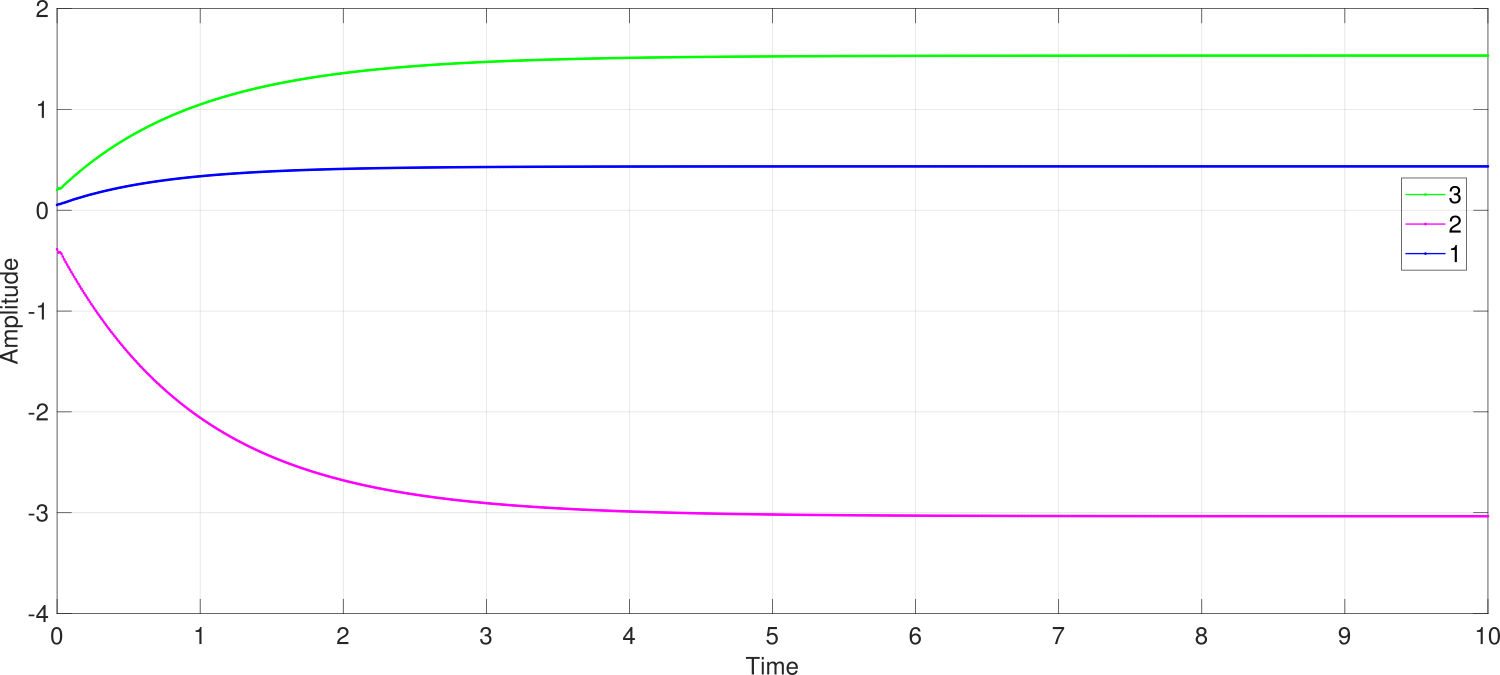
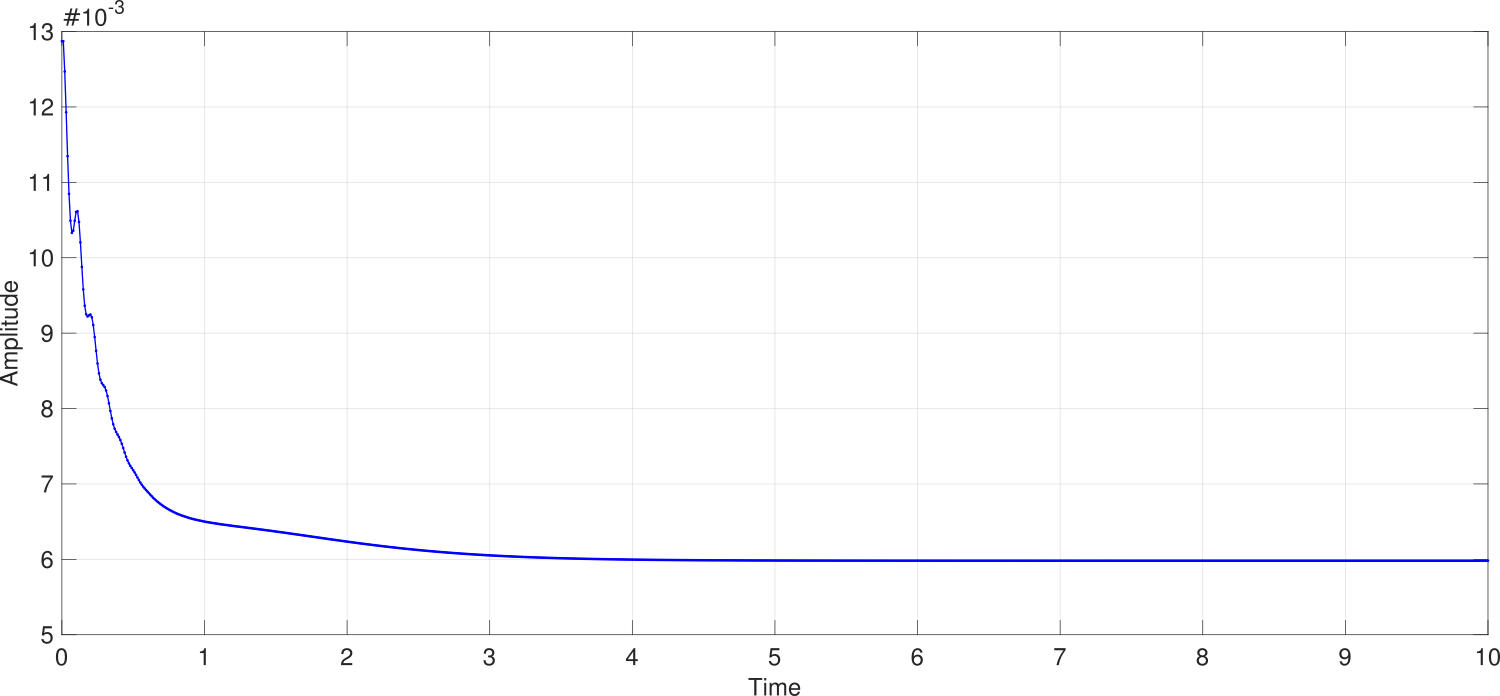
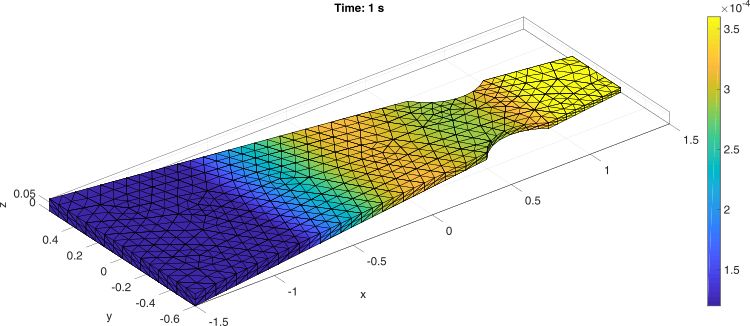
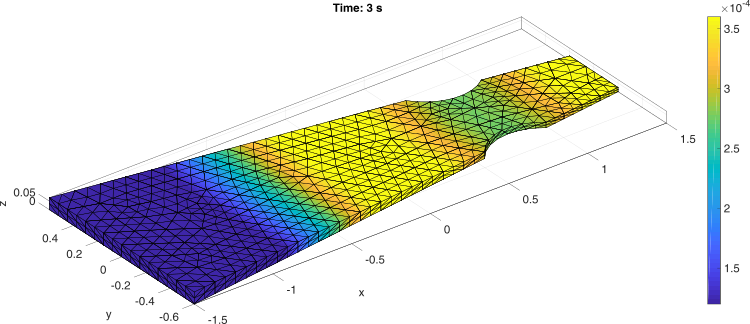
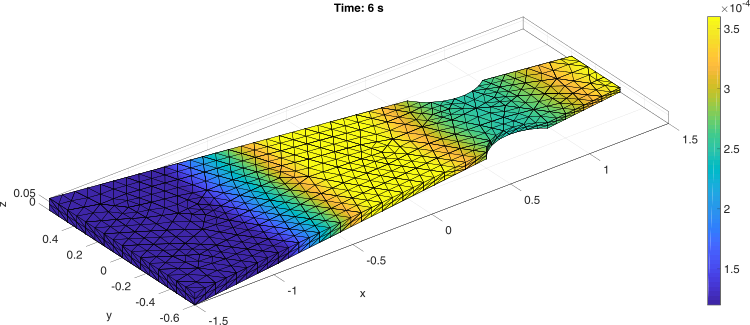
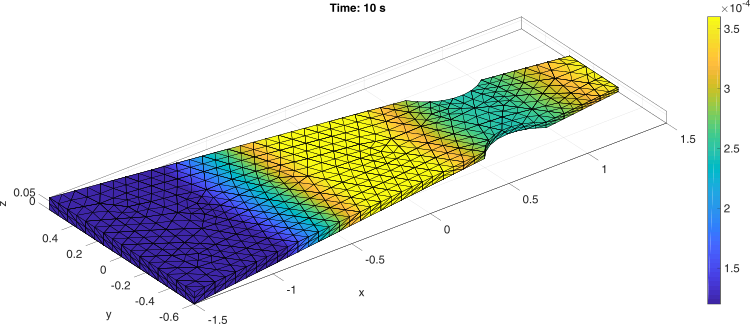